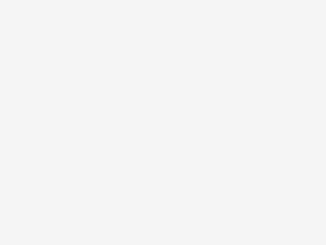
the latest generation of Porsche diagnostic tool
Porsche vehicles are renowned for their performance, engineering, and unparalleled driving experience. To ensure optimal maintenance and troubleshooting, Porsche enthusiasts and technicians rely on advanced […]